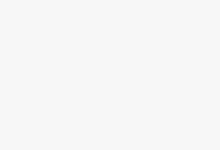
Weaving the digital world, the server power industry is at the time
In the digital age, the demand for server power is rising. What new challenges will server power companies and magnetic component companies face?
Editor’s note: In the 5G era, information data has exploded, and more and more data centers have emerged. The latest data from Synergy Research, a market research organization, shows that as of the end of the second quarter of 2021, the total number of large data centers has increased to 659.
Thanks to the rapid growth of data centers, weaving has become a digital world, and the demand for servers has also increased. According to IDC’s “China Server Market Tracking Report for the Second Quarter of 2021”, China’s server market shipments in the first half of the year were 1.706 million units, an increase of 8.9% year-on-year; the market size was 10.81 billion U.S. dollars. According to the data from the enterprise search, there are 60,600 existing server-related enterprises in my country. In 2019, 7,135 new companies were added, a year-on-year increase of 20.89%. There will be 7,242 new companies in 2020, a year-on-year increase of 1.50%. The apparent increase in the number of server companies in recent years also reflects from the side that the server industry is in a period of rapid development.
The development of the server industry is inseparable from server power. So, in the 5G era, how does the server power supply improve in performance? What are the requirements for magnetic materials and magnetic components? What is the future development direction of server power supply? With the development of third-generation semiconductor materials, will GaN be widely used in server power supplies in the future?
With these questions in mind, this issue of “Magnetic Components and Power” has a “Dialogue” column. We have invited representatives from many domestic power supply companies, magnetic component companies, and magnetic materials companies in the field of server power supplies to discuss the above issues. Practitioners who have been deeply involved in this industry have a better understanding of the ecology of the server power supply industry to provide tips within their capabilities.
Dialogue guide:
In the 5G era, the performance of server power supply changes? What are the higher requirements for magnetic materials and magnetic components?
In response to the high-frequency requirements of the above-mentioned server power supply companies, can the magnetic component companies meet?
Miniaturization has become the future development trend of magnetic components. How can magnetic component companies meet?
How can companies strengthen the quality control of magnetic materials? Are you increasing investment in research and development of new magnetic materials?
The technical difficulties of server power supply and the future development direction?
Are magnetic component companies transforming towards automation and digitalization?
What measures can magnetic component companies take to better ensure the completion of production within the delivery period?
Dialogue guests:
What do you think of the development of the server power supply market?
The Great Wall of China Wang Yongan: The server power supply market is in a rising period, and the business volume of server power supply has increased significantly. We generally produce fixed power modules with different power frequency bands, and then customers can combine them according to their needs. Generally speaking, the cost value of magnetic components is about 8% of the total cost of the power supply.
Manager of the server power supply enterprise section: Our company has made a long-term technical reserve in server power supply modules, and has achieved batch shipments to the domestic and foreign markets. The era of big data has begun, and the market’s demand for server power is also increasing year by year. We believe that data center construction is also within the scope of the country’s new infrastructure, and the market demand for server power will continue to be strong in the next few years. In addition to the growth of the domestic market, as far as the customers we have contacted, there are also many orders overseas, so we are also very optimistic about the development of the server power supply market.
Magzine: With the construction of infrastructure such as 5G base stations and data centers, the demand for server power supplies has grown rapidly in recent years. Many small-sized magnetic components produced by our company are used in the field of server power supplies, and the business has grown significantly .
Jingang Magnetics Liu Feng: Nowadays, the demand for digital storage is increasing, and the speed of information transmission is also required to be faster and faster. While bringing us a broad market, it also puts forward higher performance requirements for magnetic materials, magnetic components, and server power supplies.
What is the power range of the server power supply? What are the magnetic components used in each power module?
Kangshu Electronics Wang Fengwei: The current server power supplies have large, medium and small frequency bands, so power modules will be produced according to different power frequencies. Most of the power modules used in cloud servers are in the range of 300-1200W. A single power module probably needs 4 Electronic transformers and 5-6 inductors. The total cost of magnetic components in the power module can reach one or two hundred yuan. Therefore, we will pay more attention to the issue of controlling the cost of magnetic components.
Delta Zhang Huichang: The power range of the server power supply ranges from 300-3000W. It does not say that there is a specific standard wattage, and more is to produce power modules that meet their power frequency bands according to the needs of customers. As far as a single power module is concerned, various types of magnetic components, such as common mode inductors, differential mode inductors, PFC inductors, filter inductors, and isolation power transformers, will be used, and there are about 8-10 pieces.
Server power supply enterprise section manager: The server power supply of the small and medium power section is mostly 350W-1000W. From a single power supply module, the cost of magnetic components can reach 10%-13%.
In the 5G era, the performance of cloud server power supply changes? What are the higher requirements for magnetic materials and magnetic components?
Kangshu Electronics Wang Fengwei: As the frequency of server power is getting higher and higher, we will choose more high-frequency, low-loss magnetic materials and magnetic components.
From the perspective of the production process of magnetic components, electronic transformers basically use a PCB board plus a ferrite core structure to replace the traditional winding solder, that is, more flat-panel transformers are used. Secondly, it is now Industry 4.0 under big data, and many labors in the electronics manufacturing industry are gradually being replaced by equipment. For example, a traditional transformer requires more than one hundred people to produce, and now only 8-10 people are needed to work, and it can have a production capacity of nearly 20k. Therefore, we will ask our magnetic component suppliers to develop in the direction of automation and digitization.
Wang Yongan of the Great Wall of China: Magnetic components must move toward high frequency, and the most important thing is to achieve technological breakthroughs in magnetic materials. This year, we launched a new type of magnetic material, which can not only meet the needs of server power supply, but also meet the needs of high frequency and low loss of magnetic materials in various fields such as 5G base stations, new energy, smart homes, and optical storage and charging. One or two months The experimental work has just been completed and is preparing to market.
Server power supply enterprise section manager: Compared with 4G, the main feature of the server power supply in the 5G era is high power density, which requires small size, high power, and high efficiency. In order to achieve these performance requirements, on the one hand, it is necessary to integrate magnetic components, such as power transformers, power inductors, and CTs. On the other hand, the application of new magnetic material structures and materials, such as the magnetic core structure for heat dissipation hole design, the use of improved 95 or even 96 materials.
Delta Zhang Huichang: This year our company used gallium nitride in power modules for the first time in accordance with customer needs, which greatly increased the operating frequency of cloud server power supplies. But this also requires our magnetic materials and magnetic components to do the relevant cooperation. Among the magnetic components, taking the electronic transformer as an example, its working frequency will be increased to about 100khz, which is also the best working frequency that can be achieved by conventional magnetic components. However, in the future, it will continue to develop in the direction of high frequency.
In response to the high-frequency requirements of the aforementioned cloud server power supply companies, can magnetic component companies meet?
Haiguang Electronics Ouyang Shunchang: Conventional magnetic components can reach 100khz and above. I think GaN may indeed be used in cloud service power supplies in the future. In fact, there are already some materials that can reach a frequency of 1 MHz, but they have not yet been mass-produced, but from a technical perspective, it is not a problem.
Klick Wang Huan: Whether it is a transformer or an Inductor, it can now reach 100khz. High frequency is the development direction of magnetic components in the future. Nowadays, silicon carbide has been widely used in various terminal fields, and gallium nitride is likely to be used in server power supplies in the future, and it is expected to reach 500khz by then. To reach 1 trillion, both magnetic components and magnetic materials will be improved accordingly.
Jingweida Wang Hongwei: At present, the application range of planar transformers is 100kHz~1MHz, and 500kHz planar transformers can be designed and mass-produced. We have done technical research on the laminated structure of 500kHz~1MHz planar transformers and the application of magnetic materials. Planar transformers can meet current and future designs and applications in the next 10 years. Different magnetic integration technologies are used to increase power density. GaN is the direction to increase power in the future. Cooperating with planar transformers as servers can effectively increase power density.
Hangjia Chiyuan Manager Xiao: We have built a special magnetic component performance testing team. In addition to high frequency, magnetic components must also be small, so that the power module can meet the needs of large currents with limited space or unchanged volume. How do magnetic component companies meet?
Haiguang Electronics Ouyang Shunchang: Miniaturization has been a major trend in the development of the magnetic component industry, not only server power supplies, but many power supply companies and end customers will have miniaturization requirements. Therefore, almost all of our magnetic components will be flattened in the design, such as flat-panel transformers, etc. will also be used more on server power supplies.
Klick Wang Huan: In fact, most of the magnetic components we have introduced have been flattened in size, while achieving high power density and high current. This is mainly due to our re-structural design of magnetic components and the introduction of products that are more adapted to the trend of miniaturization, such as planar transformers. In addition, for server power supplies, we will also choose some new materials to reduce product volume.
Jingweida Wang Hongwei: The application of planar transformers and magnetic integrated technology magnetic devices can effectively reduce the volume of magnetic components.
Kangshu Electronics Wang Fengwei: We have always attached great importance to the quality control of magnetic materials, such as the problem of dark core cracking. With the subsequent development of server power supplies, existing magnetic materials are likely to be replaced by new materials with higher power and lower loss. (How can companies strengthen the quality control of magnetic materials? Are they increasing investment in research and development of new magnetic materials?)
Klick Wang Huan: For the quality control of magnetic materials, we will conduct reliability verification. For example, in the production process of dispensing, we will control its dispensing volume, dispensing time, etc., after repeated experiments, debug appropriate parameters and then carry out large-scale production. There will be further tests on the products produced. Through multiple experiments and testing in the early and late stages, the quality of product production is improved. For server power supplies, we are currently developing a ferrite material that is resistant to high temperatures, has a smaller volume, and a higher saturation magnetic flux density.
Delta Zhang Huichang: Our company is developing new magnetic materials for server power supplies. Like the previously commonly used materials of 95 and 96, it has gradually been unable to meet the demand for high frequency, and more high frequency materials will be developed later.
Haiguang Electronics Ouyang Shunchang: Dark core cracking is a common core problem. We are also very concerned about quality issues in this area, so when the supplier provides it, we will also use testing equipment for experiments and testing, and will only be used if it meets the quality requirements.
The Great Wall of China Wang Yongan: This year we have made breakthrough technological progress in magnetic materials, and completed the experimental certification one or two months ago. This newly-launched magnetic material has the outstanding advantage of high operating frequency, conforms to the current development trend of high-frequency server power supply, and can also be applied to various electronic terminal fields. Nowadays, some power modules use gallium nitride. Although it is claimed that the frequency can reach one megahertz, the actual application has not reached it. The reason is that the magnetic materials used do not match, which reduces the efficiency of gallium nitride. This new type of magnetic material can adapt to the frequency of use of gallium nitride, that is, when the operating frequency of gallium nitride reaches 1 MHz, the entire power module can also achieve an operating frequency of 1 MHz, giving full play to the maximum efficiency of gallium nitride.
Liu Feng from King Kong Magnetics: The dark core cracking is a common bottleneck hidden danger in the industry. Therefore, we generally optimize and upgrade from the sintering process and molding equipment. However, limited by current technology, it is still impossible to avoid cracking during sintering or molding, which requires us to perform appearance selection in the later stage. Our company can automatically sort through CCD appearance inspection equipment to ensure that the products provided to customers are high-quality and high-performance products.
The technical difficulties of server power supply and the future development direction?
Kangshu Electronics Wang Fengwei: We have been deeply involved in the field of server power supply for many years, and we have also paid great attention to research and development. Basically, all the technical difficulties in this field have been overcome, which can meet the needs of servers on the market. In the future, based on the characteristics of 5G and the development of gallium nitride technology, we will make appropriate technical reserves, develop or select new magnetic materials, and improve design capabilities and production processes. We also hope that upstream magnetic material companies and magnetic component companies can follow the direction of our future development and continue to develop in the direction of automation, digitization, and intelligence.
Delta Zhang Huichang: We have overcome the traditional technical difficulties. But technology is a thing that changes with each passing day, and there is no end to it. For example, this year’s power module tried to use gallium nitride solution, so there will be new technical difficulties. The customer’s requirement is not only high frequency, but also high Bs value and miniaturization. It is a new technical challenge to magnetic materials and magnetic components that can not be magnetically saturated while maintaining high frequencies.
According to the current pursuit of customers, server power supplies and magnetic components will go in the direction of high-frequency miniaturization and cost control in the future. Secondly, the application of third-generation semiconductor materials such as gallium nitride may also increase. However, after the high frequency, the temperature will increase, so a new strategy must be adopted in terms of heat dissipation. At present, we can only use gallium nitride when customers have relatively strict design and space requirements, so it is more customized production. Mass production will gradually occur after subsequent cost drops.
Delta Zhang Huichang: We will consider many aspects when choosing a magnetic component company, among which product quality is our biggest concern. For the stability of product quality, we will choose more magnetic component companies with high level of automated production. (Is the company transforming towards automation and digitalization?)
Jingang Magnetics Liu Feng: Now our company can basically achieve automation from the front-end molding to the sintering to the back-end processing. And in the past two years, it has been actively transforming in the direction of digitalization.
Klick Wang Huan: In the early design stage of magnetic components, we will consider the needs of later automated production to design. In the past two years, we have also introduced some new production processes to better meet the needs of automated production of magnetic components and greatly improve the level of automated production.
Kangshu Electronics Wang Fengwei: We will pay attention to the issue of whether magnetic component companies can deliver on time. For this reason, it is hoped that magnetic component companies can increase production capacity and have a certain amount of inventory. (What measures can magnetic component companies take to better ensure the completion of production within the delivery period?)
Klick Wang Huan: First of all, we will prepare materials in advance for different products based on previous years’ experience and customer needs. Secondly, although our own production capacity is sufficient to cope with the delivery time proposed by customers, it may be delayed due to the influence of upstream suppliers. Therefore, we will expand our existing supplier selection and increase alternative suppliers to maintain the supply of goods. Stabilize and reduce the occurrence of forced delivery extensions.
Jingang Magnetic Industry Liu Feng: First of all, we will first clarify their demand information with customers, and grasp our production direction and production rhythm. Second, we will have proper material preparation. It’s just that this year, affected by the price increase of raw materials, we will be more cautious in preparing materials. Third, we will increase and expand production appropriately according to market demand. However, judging from the current market situation, our production capacity still has some spare capacity, so we can meet the requirements of timely delivery.
Server power supply enterprise section manager: Magnetic components are the key to the composition of power modules, so controlling the design cost of magnetic components has become a top priority. (How can companies better reduce costs and maximize corporate benefits?)
Jingang Magnetic Industry Liu Feng: This year, affected by the national policy and trade environment, the rise in raw materials has brought great cost pressure to enterprises. For this reason, there are mainly two directions to control our costs. On the one hand, it can improve the quality and pass rate of our products and reduce losses. On the other hand, it improves production efficiency and shortens the production cycle. To do this, we need to improve our automated production level.
Klick Wang Huan: Generally speaking, the prices of resistors and capacitors are relatively stable, while there are more customized production of magnetic components, and there is more room for price fluctuations. In order to better control costs, we will consider later automated production when designing the front-end of magnetic components, thereby improving the level of automated production. Third, the cost of loss can also be reduced by improving the product yield. For the key front-end processes, such as soldering process, in the past two years, we have used resistance welding heating method to weld, replacing the original tin bar welding, not only the product yield rate has been greatly improved compared with the past, but also reduced The generation of pollutants conforms to the trend of today’s green production.
Jingweida Wang Hongwei: Cooperate with customers to increase the power frequency, effectively use magnetic integration technology, and reduce the use of magnetic materials. Minimize the amount of materials used in the design, optimize the design to reduce the man-hours of magnetic components, and improve production efficiency.
Conclusion:
The increase in the number of data centers in the 5G era has driven the development of the server industry, and has also brought broad market development space to server power supply companies, magnetic component companies, and magnetic material companies.
A report from the Big Bit Industry Research Office shows that in mainstream X86 servers on the market, there are an average of 6 customized inductors and 4 electronic transformers in each power module, and there are nearly 50 magnetic components in the circuit board. At present, servers on the market are dominated by a model with 2 power supplies and 4 power supplies. The average value is calculated based on 3 power supplies for each server. There are about 80-100 magnetic components in a server. It is estimated from this that there will be a demand for 1-12 billion magnetic components in X86 servers worldwide in 2021, and there will be a demand for 1.7-1.9 billion magnetic components by 2025.
However, it is not easy to get a share in this market. Especially in the past two years, under the dual influence of the outbreak of new infrastructure demand and the supply of the epidemic, magnetic component companies sometimes fail to supply them in time. This has become an important inspection method for server power supplies when choosing companies today. In order to be able to deliver in time, companies can meet customer needs from the following four aspects: one is to clarify the needs of customers, including the specific order quantity and final delivery time; the second is to properly stock raw materials; the third is to expand upstream supplier selection , Diversify risks, and ensure that upstream companies can provide sufficient supply; fourth, expand production and increase production in a planned way.
From the sharing of the guests, we learned that with the development of server power supplies, higher frequency and miniaturization requirements have been put forward for magnetic materials and magnetic components. For this reason, magnetic material companies and magnetic component companies have also chosen to actively challenge, continuously increase their investment in research and development of new magnetic materials, and reduce the volume through structural redesign, and continue to move towards high frequency while meeting the current 100khz conventional requirements. Make a breakthrough.
In addition, some server power supply companies have realized the application of gallium nitride materials to power modules this year. Talking about the future development direction, most magnetic component companies and server power supply companies believe that with the development of third-generation semiconductor materials, the application field of gallium nitride materials will be more extensive, and the application in server power supplies will also be Go deeper. For this reason, many companies have revealed to reporters that the company is currently making relevant technical reserves to cope with this trend.
The Links: G185XW01-V201 MBM150GS12AW LCD DISPLAY