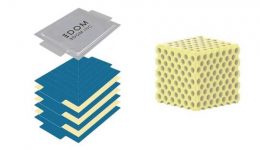
Beginning with “double energy density” lithium metal batteries: accelerating the layout of next-generation battery production capacity
“At present, the negative electrode of lithium-ion batteries mainly uses carbon materials, while 3DOM uses lithium metal. Although the latter is easy to increase the capacitance, it also has the risk of short-circuit and fire. The cause of the fire is the phenomenon of dendrites, which are columnar crystals grown on the surface of the negative electrode due to unbalanced chemical reactions.
“
Even with the world’s most powerful car brand, Europe has fallen behind Asia in terms of new energy, especially power batteries. For this reason, with the support of the government and industry, Europe is catching up.
In October 2020, the start-up company Lavle stated that it is building a super factory that will mass-produce next-generation battery modules in the United States before the end of 2023, with a final production capacity of approximately 7GWh per year. It is said that the next generation of technology will completely change the face of aviation, shipping, railway, national defense and oil and gas industries. A new era of battery-powered airplanes, ships and trains may begin in the next few years, thanks to the mass production of advanced lithium-metal batteries with twice the energy density of traditional lithium-ion technology.
It is undeniable that even with the world’s most powerful car brand, Europe has fallen behind Asia in terms of new energy, especially power batteries. For this reason, with the support of the government and industry, Europe is catching up.
Large-scale construction of European and American super factories
In the past two years, news of the construction of super factories in Europe and the United States for the production of various energy storage batteries spread like wildfire, aiming to grab a lot of lithium batteries and prepare for the future of decarbonization.
In November 2019, when German automakers invested heavily in electric vehicles and batteries, Tesla announced that it would build Tesla’s German R&D center in Berlin and plans to build a super factory in Greenheide. It has been approved by the German Federal Ministry of Economics and Energy. The plant will produce a new 4680 battery with a 5 times higher energy density and 6 times higher power than existing models, which will take up less space and consume less energy.
In April 2020, the start-up company Tesvolt opened a photovoltaic cell factory near Wittenberg, Germany. The factory covers an area of 12,000 square meters and can produce 1MWh energy storage systems every day. It is said that it will be the first super factory in Europe to produce commercial battery energy storage systems, with an annual output of more than 1GWh.
In July 2020, the Swedish battery company Northvolt raised US$1.6 billion for a European lithium-ion battery factory and is building one of Europe’s largest battery factories in Skelleftea, Sweden. Contend with Asian battery companies.
In August 2020, French battery manufacturer Verkor announced that it will open and operate a lithium battery production plant with an annual output of 16GWh in France in 2023, and expand its annual output to 50GWh according to market development. The company’s batteries will be used in electric vehicles (EV) and stationary energy storage.
Peter Carlsson, co-founder and CEO of Northvolt, said: “The momentum of electrification is stronger than ever. Our customers need a large number of high-quality batteries with low carbon dioxide emissions, and Europe must establish a completely regional The value chain to support them.”
U.S. Gigafactory ambitions revealed
Going back to the next-generation battery module super factory in the United States at the beginning of this article, it is reported that the millions of dollars in funding for this 1.5 million square foot (14 hectare) facility have been “basically in place.” Lavle Chief Technology Officer Dr. Ben Gully explained that doubling the energy density of lithium-ion technology will create a lot of opportunities. Prior to this, he led the research on lithium-ion battery safety in the maritime advisory group of DNV-GL, laying the foundation for the formulation of the world’s highest lithium-ion battery safety standard.
According to reports, Lavle is designing and preparing a prototype energy storage system for its large-scale lithium metal battery (LMB) and solid electrolyte battery (SEB) energy storage systems. The system uses batteries developed and provided by 3DOM in Japan.
The use of lithium metal as the negative electrode of a battery is called the “Holy Grail” of battery technology. The benefits it provides far exceed the use of solid electrolyte alone, and the energy density produced is much higher than other current commercial lithium-ion batteries. Large-capacity batteries with these characteristics are already in operation in 3DOM and Lavle laboratories.
These batteries use 3DOM’s diaphragm technology, which not only benefits the functions of LMB and SEB (passivation batteries) batteries, but also makes these batteries much safer than the most advanced lithium-ion batteries. Lavle’s SEB and LMB technologies have achieved an energy density of 420Wh/kg in full-size large-capacity batteries, which is more than twice that of traditional lithium-ion batteries. Compared with competing solutions that require high temperatures, Lavle’s LMB and SEB can provide the safety features necessary for a wide range of commercial applications at an ambient temperature of 25°C.
Gully explained: “If you have an electric car with a range of 300 miles, you can use a battery of the same size and weight to turn into an electric car with a range of 600 miles. Or if you only need 300 miles, then you can put The weight of the battery is halved, so your car will perform better. As you can imagine, energy density opens up new applications and battery use cases that we can’t even imagine now.”
He said that once the supply chain is established and the battery is produced on a large scale, its lithium metal batteries will be able to achieve the same cost per kilowatt-hour as traditional lithium-ion batteries. However, the company is currently not keen on getting involved in the highly competitive and low-margin electric vehicle battery field. “In other markets, the benefit of energy density is to change the rules of the game and develop viable products and systems. Without it, it would be impossible,” Gully added.
Emerging applications are coming
Morten Pedersen, chief operating officer of Lavle, said that medium-distance deep-sea shipping is a scenario for this new type of battery application. .”
Another possibility is electric aviation. He added: “In Europe, “most flights have a flight time of less than 30 minutes. Therefore, for such flights, lithium metal batteries have a large number of applications. Several airlines have indicated that they want to fly 650 miles (1046) with 900kWh batteries. Kilometers). This usually requires a 20-foot container, so you can’t fly that far today. But our batteries can do that.” In theory, this would allow businesses to fly from London to Prague (1033 kilometers) The flights use renewable energy batteries.
It is reported that this kind of high-energy density battery has attracted the attention of the defense industry because it may carry out long-distance, almost silent flights without thermal characteristics. The company said that it is currently in discussions with a “research-oriented military organization”, but it is understandable that it refuses to provide details.
Similar opportunities have also emerged in the railway, oil and gas industries, and the emerging electric truck sector. Hybrid and full battery electric propulsion can be promoted in new marine and defense markets, including high-speed ferries, long-haul ferries, shuttle container ships, cruise ships, frigates, destroyers, submarines, and automatic underwater vehicles (AUV), etc.
Security is unmatched
Undoubtedly, one of the shortcomings of traditional lithium-ion batteries using carbon materials for the negative electrode is that they may catch fire, which is a potential hazard for deployment on airplanes, ships, trains, and oil rigs.
In 2019, 23 battery energy storage system (ESS) fires occurred in South Korea’s wind and solar power plants within one year, involving suppliers such as LG Chem and Samsung SDI. After months of investigation, the Korean Ministry of Industry concluded: battery protection Insufficiency, inappropriate operating environment, installation errors and system-level problems are all at work, and a series of new control measures have been introduced.
As early as 2012, just one year after it was put into operation, the fire destroyed the largest Hawaiian wind energy storage system in North America, and a fire destroyed a 15MW battery pack.
It is no coincidence that Lavle has focused on technology to prevent such incidents. Gully said: “The level of safety we provide and develop is an inherent feature of the system, which is basically unparalleled in the industry. When you install 4-5MWh on a ship with 50 passengers separated by a wall, all The level of security required is very different.”
Pedersen added: “If you look at the large freight trains in the United States, some trains are a mile long. If one of them breaks because of a problem with the (battery-powered) locomotive, it will block many road intersections and cause serious chaos; it Transport fuel or coal frequently-you don’t want to catch fire too close. In terms of national defense, it may be a mission-critical thing, or it may be related to the safety of soldiers.”
As we all know, the strength of the battery depends on the weakest link in the chain, and Lavle’s advanced battery management system (BMS) has a “dual redundancy design throughout the entire ESS, which can ensure that a single component failure anywhere in the system will not cause more than “The failure of a battery string”, its passive and active balancing solutions can completely alleviate any unexpected situations.
Its BMS uses a second-generation, proven design that has been extensively tested, and its safety features include:
An efficient thermal management system that completely alleviates thermal runaway, with high-performance liquid cooling, optimized battery chemistry, and multi-layer transmission barriers to prevent mischarging from causing the battery to overheat and catch fire;
Each battery has dual redundant voltage sensing to ensure accurate voltage detection and prevent accidental overcharging;
Novel gas and leak detection technology, including dual gas release valves and exhaust detection in each module, as well as full cabinet ventilation management, no one in the industry provides;
High-precision dynamic state of charge (SOC) calculation to ensure optimal operation and aging control;
The high-performance active and passive balance system ensures the maximum utilization of available capacity and improves the life and reliability of the system;
Highly secure remote monitoring and cloud-based data services allow the battery system to provide the highest level of support and performance;
Rear blind mate connection can eliminate the risk of arc flash and eliminate messy cables;
The module is fixed on the rack and has a screwless integrated locking mechanism, which is easy to clean and install.
The origin of lithium metal battery technology
The lithium metal battery was developed by Lavle’s joint venture partner 3DOM (which holds a majority stake). The latter is a start-up company established at Tokyo Metropolitan University in 2014.
According to Gully’s explanation, 3DOM’s next-generation patented technology is basically a lithium-ion battery. The difference is that an electrode made of lithium metal replaces the traditional graphite negative electrode.
He admitted that other companies are also developing similar batteries in the laboratory, but 3DOM and Lavle are far ahead of the competition. He said: “To make it work, the key is the rest of the system, as well as the design of the battery, the electrolyte, etc.-getting all these things to work together is a challenge,” he said.
The characteristics of Lavle’s new generation of lithium-based ESS are all derived from the 3DOM diaphragm. 3DOM is a new type of diaphragm technology development company, and the diaphragm is the separator between the positive and negative electrodes of the battery. Electrons flow between the positive and negative electrodes through the film, generating electric current to do work. The 3DOM diaphragm is made of polyimide resin with high heat resistance. The diaphragm spheres are neatly arranged with a diameter of hundreds of nanometers. Due to the uniform size of the holes and orderly arrangement, the ions flow uniformly and the chemical reaction is uniform, which can prevent thermal runaway (overheating), so that the battery has inherent safety and will not burn even at a high temperature of 400°C.
3DOM’s technology has passed various reviews by Tokyo Metropolitan University in Japan, and has been supported by the New Energy and Industrial Technology Development Organization (NEDO) of Japan.
Research directly refers to the formation of lithium dendrites
At present, the negative electrode of lithium-ion batteries mainly uses carbon materials, while 3DOM uses lithium metal. Although the latter is easy to increase the capacitance, it also has the risk of short-circuit and fire. The cause of the fire is the phenomenon of dendrites, which are columnar crystals grown on the surface of the negative electrode due to unbalanced chemical reactions.
As early as February 2012, the 3DOM high-rate performance polyimide separator for rechargeable lithium batteries researched by Kazuhei Miyahara, Yongcheng Jin, Hirokazu Munakata and Kiyoshi Kanamura of the Department of Applied Chemistry of the Graduate School of Urban Environmental Sciences, Tokyo Metropolitan University Presented at the ECS (American Electrochemical Society) meeting.
The paper pointed out that metallic lithium is the one with the largest capacity and the lowest oxidation-reduction potential among various anode materials. Therefore, it is expected to become an ideal anode material for next-generation batteries. So far, there have been many researches on using metallic lithium as rechargeable lithium batteries. However, due to the low cycle and safety problems of lithium-ion batteries, lithium-ion batteries have not been practically used (now practically used, but there are still problems with safety), which is the same as the morphology of lithium-ion batteries deposited during the charge and discharge cycle related. In particular, the dendritic morphology of lithium metal reduces the rechargeability and safety of the battery. In the process of metal lithium deposition, dendrites are formed due to the large current distribution. This large current distribution is caused by the unevenness of the lithium metal surface.
The paper believes: “In order to inhibit the formation of lithium dendrites, the surface state of lithium metal must be controlled and stabilized. In previous work, we found that the use of a separator with a three-dimensional ordered macroporous (3DOM) structure can inhibit the formation of dendrites. “
According to the paper, the porosity of 3DOM diaphragm is very high, about 70%, which is twice the porosity of conventional polypropylene (PP) diaphragm. In addition, the size and distribution of pores in the 3DOM diaphragm are very uniform. This superior structural characteristic realizes the practical application of lithium metal anode, which is expected to be used in conventional electrode materials to improve the safety and rate performance of the battery. Through in-depth research on the conductivity of lithium ions in the 3DOM separator, the structural advantages of its rate performance have been proved in the charge and discharge tests of rechargeable lithium metal batteries.
Three-dimensional ordered macroporous structure of 3DOM diaphragm
The 3DOM membrane prepared by experimental polyimide is like a honeycomb, with monodisperse silica beads with an average particle size of 300nm arranged in an orderly manner. The uniform pores prepared by the colloidal crystal template method realize the overall uniform chemical reaction.
In the study, the performance of the 3DOM separator was evaluated with 2032 button batteries, and two types of cell configurations were used. One is the symmetrical configuration of lithium metal/3DOM diaphragm/lithium metal. The other is a lithium metal/3DOM diaphragm/LiNi0.8Co0.15Al0.05O2(NCA) composite material with an all-cell structure. The NCA composite material polyvinylidene fluoride (PVDF) was prepared by pouring the NCA-containing slurry, and the aluminum foil current collector weight acetylene black=94:3:3. The thickness of the NCA composite material is approximately 130 μm. Ethylene carbonate (EC) uses 1mol dm-3 (representing the concentration, per cubic decimeter, that is, liter) LiPF6 (lithium hexafluorophosphate): diethyl carbonate (DEC) = 1:1, as the electrolyte solution.
The results show that the pores with a diameter of about 300nm are uniformly distributed in the 3DOM polyimide membrane. The interconnection of these pores also confirms the formation of smaller pores in each pore.
Surface SEM image of 3DOM polyimide membrane
This study shows the complete battery rate performance of the lithium metal/separator (1 mol dm-3 LiPF6 in EC, DEC = 1:1)/NCA composite configuration. Using the 3DOM diaphragm, the battery can maintain a rate of up to 2.0C. On the contrary, at a higher C rate higher than 0.5C, the capacity of the PP membrane was observed to decrease significantly. This result clearly shows the superiority of the 3DOM membrane.
Superior rate performance of 3DOM diaphragm
The conclusion is: the uniform current distribution achieved by the regular structure inhibits the generation of dendrites, and significantly improves the battery life and reliability.
The company is named after 3DOM
The name of 3DOM is derived from the research results of its innovative proprietary diaphragm technology-Professor Kanamura (3DOM Director and Chief Technology Officer).
3DOM was originally a startup company founded by a university, headquartered in Yokohama, Japan. Yokohama City can be described as the “Rangshan Park” of next-generation battery research and development. It has gathered resigned scientific research personnel from various large electromechanical manufacturers and automobile manufacturers, as well as technical personnel seeking new development.
It is worth mentioning that many of 3DOM’s executives have worked at Panasonic. These people have been engaged in the lithium battery development business for more than 30 years, and have respectively served as directors of Panasonic Battery Company and general manager of the lithium-ion battery division of energy companies. They participated in the development and mass production of the industry’s first high-power lithium primary battery for cameras. , And the start of a factory that provides batteries for Tesla.
Inspired by the new business, the company originally only Professor Kanamura has attracted many engineers from large companies, and now it has more than 70 engineers.
3DOM is mainly engaged in the research and development of separators, the purpose is to suppress the precipitation of dendrites, which are the main reason for the deterioration of lithium ion batteries (LIB) and lithium metal batteries. As one of the flagship products of 3DOM, its diaphragm has been highly evaluated in terms of thermal stability and chemical stability. The uniform pore structure can prevent uneven power reactions, help suppress dendrite precipitation, and provide a uniform ion current to prevent overheating due to short circuit and fire, and ultimately achieve a significant improvement in battery performance and reliability.
The 3DOM-scale BESS system provides higher energy volume and weight energy density than traditional systems, and a longer life cycle. It also minimizes the use of cobalt, thereby reducing production costs. 3DOM BESS solutions can meet customer needs in various situations, including mining facilities, military bases, chemical plants, rice mills, airports, and oil and gas facilities. Advanced lithium-ion battery technology provides long-term reasonable and stable electricity prices.
This technology has been recognized by NEDO as a breakthrough battery technology and adopted as a Phase D project. Its goal is to commercialize promising technologies for practical use.
Accelerate the layout of next-generation battery production capacity
Within six years, 3DOM has established (including acquisition) 6 subsidiaries.In addition to using the most advanced battery technology to provide an overall solution for electrification, to promote the electrification of oil and gas ships and machinery, and to provide new batteries for the defense industry, it also hopes to introduce and download Services related to the electrification of a generation of transportation infrastructure, including: electric car rental business, air travel solutions for drones and other aircraft, blockchain application research and development, and the integration of other technologies such as the Internet of Things and artificial intelligence.
3DOM and its main subsidiaries
The goal of 3DOM’s research, development and design of next-generation batteries is to provide electricity to anyone anywhere and to deploy companies using these technologies on a global scale to solve energy problems and build a sustainable society.
Through innovations in battery manufacturing, reuse and recycling, as well as the development and deployment of applications across aerospace, navigation, mobility and storage, 3DOM is digitally changing the battery life cycle and providing a social platform for the flow of energy, people and things. , To realize the innovative business model of “battery as a service”.
3DOM’s mission
In order to cope with the commercialization of its lithium metal batteries, 3DOM is accelerating its production capacity layout and has reached cooperation agreements with many car and drone manufacturers in the United States and Europe. Currently, the company has produced lithium-ion batteries in the suburbs of Seattle, and plans to build another factory in the United States next year to prepare for the production of next-generation batteries. 3Dom’s goal is to commercialize its lithium metal batteries in 2023.
In November 2020, 3DOM Singapore and Cosmos Global signed an agreement to establish a joint venture company to establish an electric vehicle assembly plant in Bangladesh, including leasing electric vehicles, providing instant car services, and helping Bangladesh to replace internal combustion engine vehicles with electric vehicles to eliminate carbon dioxide. Emission targets.
At the same time, 3DOM also signed a memorandum of understanding with Memorandum of Understanding to provide battery products for rooftop solar solutions and battery energy storage systems for the Pathein Industrial City project in Myanmar.
Future plan
The advantage of 3DOM battery technology and 3DOM business model is that it is highly suitable for the rapid electrification of the travel market, including the era of fully autonomous driving in the future. 3DOM Representative Director Masataka Matsumura said: “We are moving from the era of computer brain creation with artificial intelligence (AI) to the digital era of DI (digital intelligence). Through a deep understanding based on individual experience and a digital grasp of conditions and situations, our The battery will connect people to people and people to machines.”
He said: “We will meet these needs as soon as possible, and by further promoting the flow of electricity and renewable energy, we will strive to close the curtain of the fossil fuel era and contribute to the protection and restoration of the global environment. In addition, we hope to become a leader in the new era. , To promote the launch of next-generation services that have not yet been realized due to the suppression of battery performance, such as new businesses that use drones.”
Gully also said: “Our long-term goal is to use the unique business model of these new generation batteries to build and maintain a battery-centric energy platform and occupy the world with lithium metal batteries. I believe that what we are doing is the most important The thing is to open the gate to possibility. The theoretical energy density we get from the lithium metal component is quite amazing. Through digital intelligence and electrification technology, it will help us create a beautiful future in harmony with nature.”
The Links: SKIIP83AC12IT1 EL320256-FD6